How to Prevent Your Parking Lot Concrete From Cracking – 2024 Guide
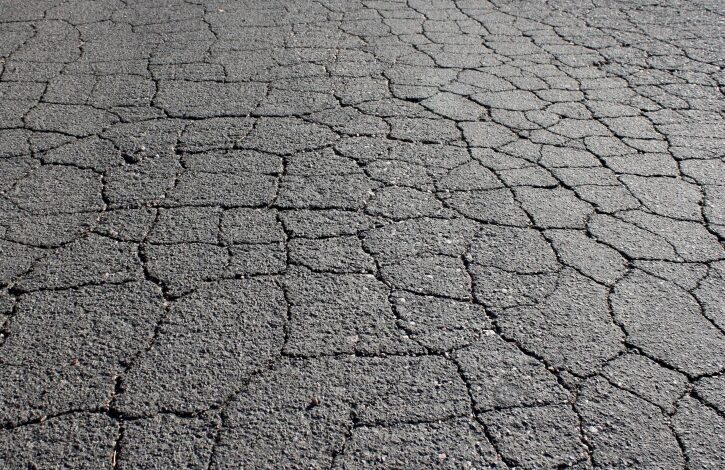
Concrete is a building material that is formed due to a chemical reaction between water and cement, which is called hydration, with the addition of aggregate in the form of sand or gravel. Thanks to this reaction, it hardens over time and connects all the components, forming a solid building material. The properties of concrete are such that due to the poor quality of construction, in a large number of cases, cracking can occur, and this often happens in parking lots. Have you ever glanced at a parking space and thought how much better it would look if the crack in the concrete didn’t give the impression that everyone who parks there will fall through the ground? Planning such unforeseen situations during the implementation of the parking project and preventive action against them can minimize the possibility of unwanted cracks. Their appearance can also affect the waterproofing and durability of concrete apart from the physical appearance. The factors that can cause their formation are various and the most common is the restraint on deformations.
Using the right admixtures or a combination of admixtures to reduce the impact of external factors can extend the life of the parking space and lead to improved performance. Read below what are the types of additives that are used for these purposes and can help you in situations like this.
The biggest cause of the problem
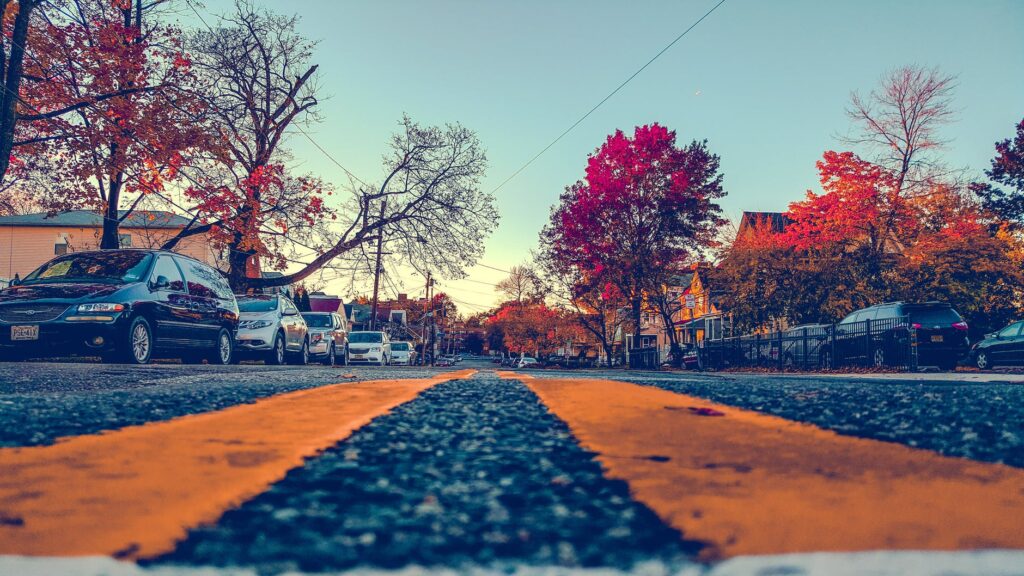
Large amounts of salt are used to prevent icy roads and parking lots in the winter. The role of salt is to melt snow and ice to minimize the chance of an accident in which someone will be injured. However, the amount of about 10 million tons per year, as research shows, is very large and has a destructive effect on all concrete surfaces with which it comes into contact.
Concrete is a material that is characterized by high porous power that allows easy penetration of water into the interior. During the winter, this water turns into snow, first, and then into ice, which doesn’t cause damage, except in the case when their retention on the roads can endanger drivers. The real problems occur after the application of salt to remove snow and ice in and to increase the safety of people.
The culmination of these problems shouldn’t be allowed and therefore we must think of a solution in time. Preventive measures that can improve the durability and resilience of the concrete base should be applied while the parking planning process is already underway, and this is achieved by adding various additives to the mixer. The whole process should be carefully carried out to the end and, on the advice of www.honolulu-concrete.com, with the help of experts whose professionally done work you can rely on.
1. Air-Entrainment
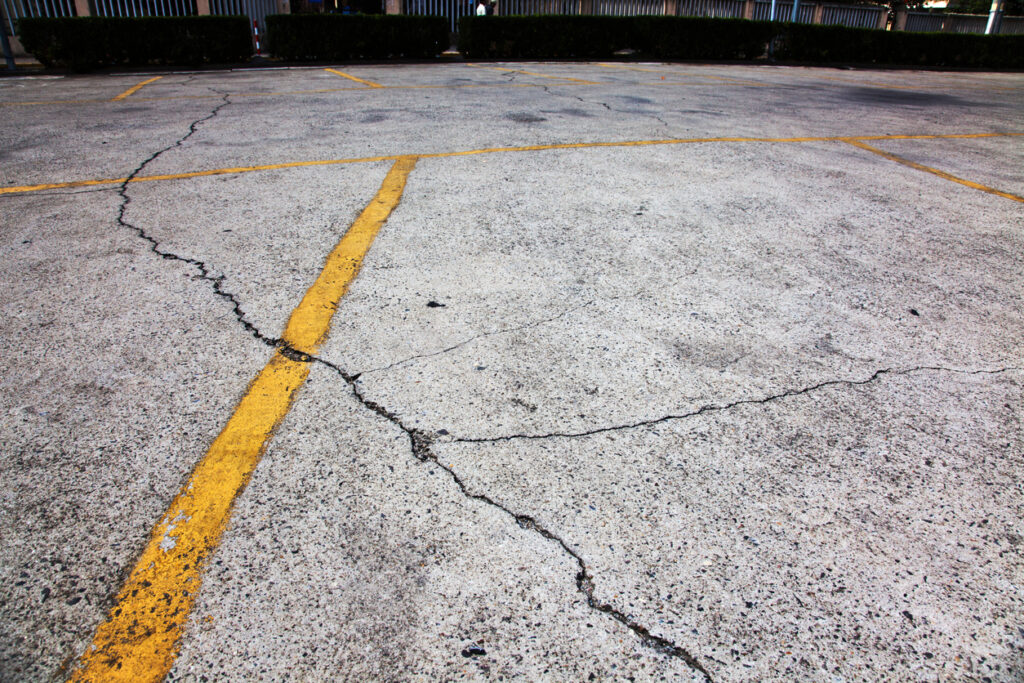
The purpose of this preventive method is to increase the durability of concrete due to low temperatures. Air-Entrainment provides increased resistance, but also a higher degree of durability and workability. The degree of resistance to pressure is inversely proportional to its workability and both parameters must be within some optimal value.
Air-Entrainment is a method that involves the process of creating small air bubbles in the concrete. This is achieved by adding various active substances whose role is to retain air bubbles. Most bubbles are formed during the mixing process.
Air retention is carried out to increase the durability of solid concrete in periods of the year when it freezes, which involves the use of salt to melt. The secondary purpose is reflected in the increase of workability in the initial stages.
For normal reduction of strength, air entrainment in the range of 3 to 7 percent is taken.
2. Accelerators
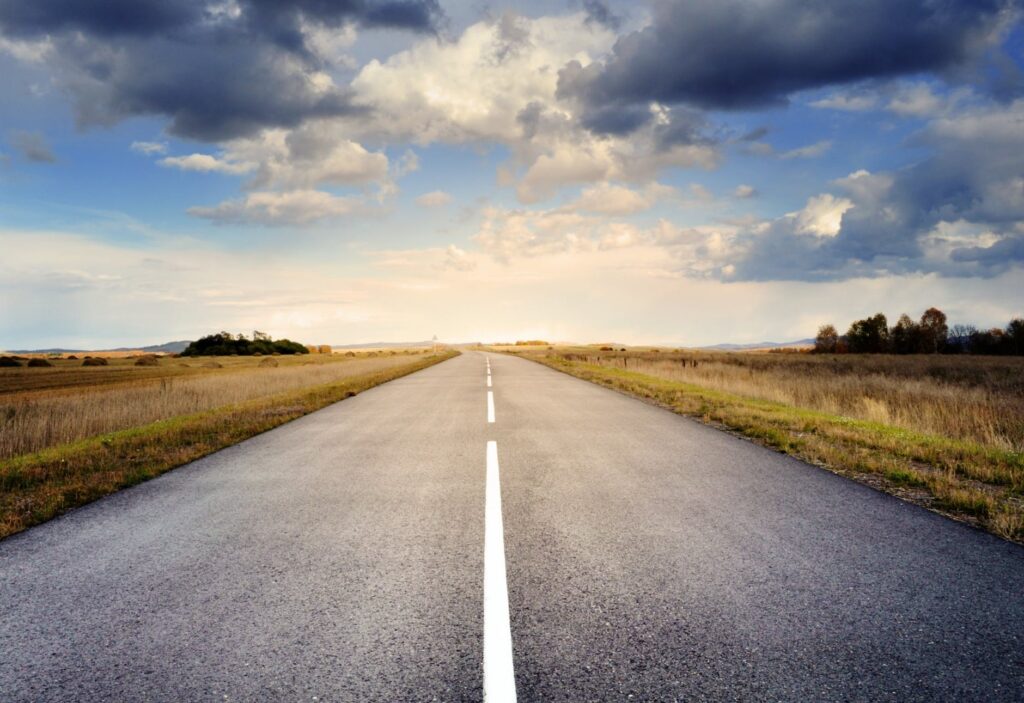
The need for pouring concrete also occurs in the winter, when the conditions for that are quite unfavorable. Exposed to low temperatures, it can be damaged by frost and therefore it was necessary to find a method that will speed up the curing process to achieve the desired resistance to these harsh conditions as soon as possible. This is how accelerators were created.
Accelerators are additives that reduce the time it takes for concrete to set and thus increase its resistance to external factors and reduce the risk of damage. Besides, the overall strength increases, and the properties change, which makes this building material easier to adapt to the cold.
Chemicals used for this purpose are calcium nitrate, calcium nitrate, calcium formate, and aluminum compounds. In the past, calcium chloride was used the most in such cases, but it was later noticed that its anions have a corrosive effect on the armature, which is why its use is no longer recommended, and in some places in the world it is forbidden.
As the best solution in recent times, there is calcium sulfoaluminate which has the power to harden within 20 minutes.
3. Corrosion inhibiting
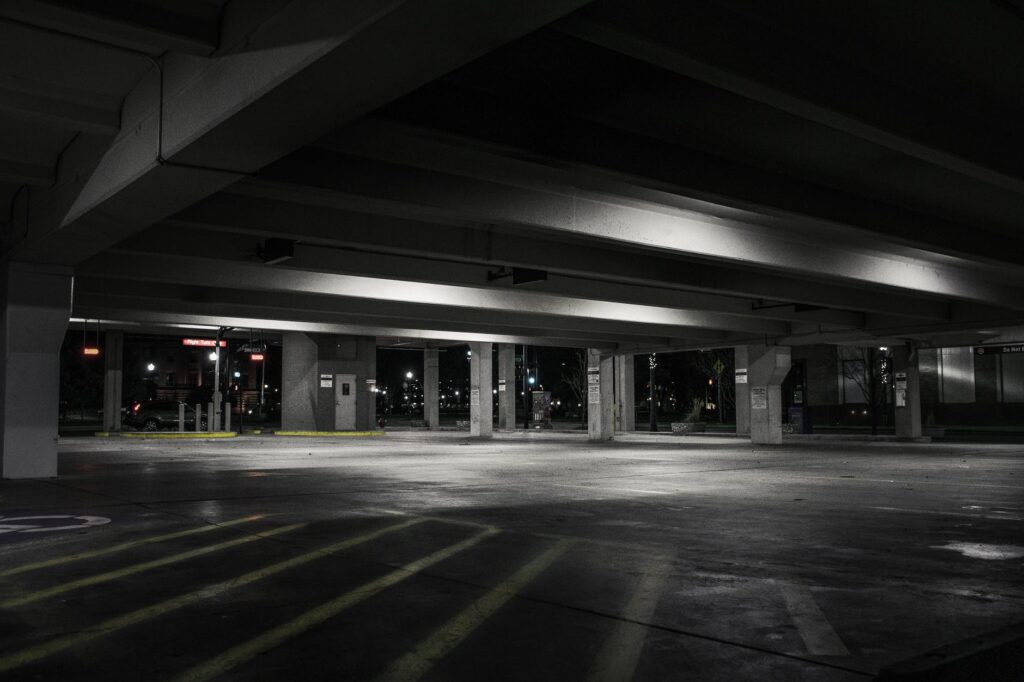
Corrosion inhibition is achieved with the help of special additives that slow down the corrosion of steel and thus significantly reduce the maintenance costs of reinforced structures. Besides, the service life of the armature is extended by 30-40 years. Corrosion inhibitors improve performance in concrete and result in increased service life potential.
Such additives act on critical points, preventing deterioration and cracking due to corrosion of the reinforcement. As we mentioned earlier, aggressive treatment with chlorides can cause such problems and your parking lot will not look like a whole for a long time, but as if it is ready to break and collapse at any moment.
An inhibitor is a chemical compound whose effectiveness depends on the amount of water, its composition, and flow. It can be found in the store in the form of a spray in combination with oil or some other substances.
The principle of operation of the inhibitor is to create a coating that prevents the corrosive substance from coming into contact with the metal – so, they are added to the liquids that surround the metal.
4. Macrofibers
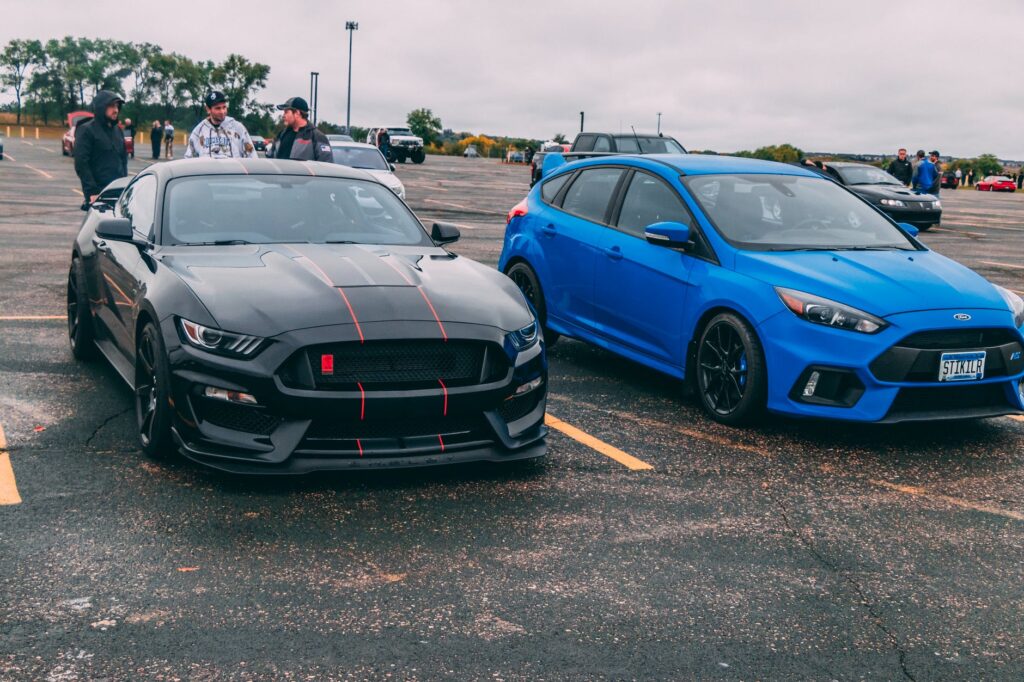
The last but not the least important suggestion are macrofibers whose role is reflected in providing superior bonding properties to the concrete matrix. In this way, good crack control is achieved and the service life of the parking lot is extended.
The chemical composition of these synthetic macrofibers consists of polypropylene resins. They are nicely distributed on the concrete mixture, giving it excellent performance and better finishing, as well as greater green strength.
Sometimes cracking concrete in a parking lot can be a big problem and a real nightmare. If you don’t act preventively against the potential damage that can occur, correcting this mistake can be much more difficult and expensive. Therefore, use some of the tips that best suit your needs and provide a long lifespan to a parking place for your four-wheeler.